Quality Assurance Process: Making Sure Things Work Right
- miriancwcw
- Jan 4
- 9 min read
Quality assurance is all about ensuring that products and services meet certain quality requirements and satisfy our needs and expectations.
It's crucial because it helps maintain consistency in the production process, which leads to better product quality, customer happiness, and trust.
In essence, quality assurance keeps the mistakes and defects out right from the start, ensuring the quality of products is up to par before they reach us.

Think about it like this: we don't want a product to break or not work as promised.
Quality assurance is the process that checks everything is in place, working smoothly, and delivered as intended.
With methods like testing, monitoring, and improving, different industries—from food to technology—use quality assurance to guarantee top-notch outcomes.
We might forget how much quality makes our lives easier, but it's everywhere.
From the software on our phones to the food on our plates, quality assurance is what makes sure everything meets the mark.
Learning more about it can help us appreciate the efforts that go into making the things we use every day.
Key Takeaways
Quality assurance ensures products and services meet high standards.
It involves testing, monitoring, and improving processes.
Quality assurance is vital in many industries to maintain reliability.
Understanding Quality Assurance Fundamentals
When we talk about quality, it's important to know the basics.
Quality assurance, control, and management each play a distinct role in maintaining standards.
Defining Quality
Quality refers to how well a product or service meets the desired standards and expectations.
It's essential to have a clear definition of quality. This way, everyone knows what to aim for.
Quality is about consistency and making sure things are right every time.
We can describe quality as a mix of features and characteristics. These might include reliability, efficiency, and ease of use.
Every detail matters and contributes to the overall experience.
Our goal is to make sure that everything, from start to finish, aligns perfectly with the expectations.
Differences Between Quality Assurance, Quality Control, and Quality Management
Quality Assurance focuses on the processes used to create products. It's about preventing problems in the first place.
By ensuring processes are set up correctly, we can build quality from the ground up.
Quality Control, on the other hand, is all about inspecting the finished product.
It's the step where we check for defects and make sure everything meets the set standards.
Think of it as the last line of defense before a product reaches customers.
Quality Management includes both assurance and control. It also involves continuous improvement.
This is about seeing the big picture. We ensure that every piece of the process, from development to delivery, runs smoothly.
Together, these elements ensure that quality is maintained from beginning to end.
Developing a Quality Management System
Creating a strong quality management system involves understanding essential components and effective planning strategies.
These elements help ensure products or services meet customer expectations and comply with standards.
Components of an Effective Quality System
An effective quality system needs several key components.
First, we set quality objectives that align with customer needs and company goals.
Clear objectives give us a target to aim for and help guide other processes.
Second, process management is crucial.
By defining and documenting our processes, we can monitor and improve them.
This allows us to ensure consistency and quality every step of the way.
Another important part is employee involvement.
Our team members play an essential role in maintaining quality. When everyone understands their role in the system, quality improves naturally.
Continuous improvement is the last major component.
We need to stay flexible and ready to adapt to new challenges or opportunities.
Regularly reviewing and upgrading our quality system keeps us on the cutting edge.
Quality Planning Strategies
Quality planning starts with setting clear, measurable goals.
Knowing what we want to achieve helps in creating a focused quality plan.
This includes identifying resources we need, from materials to team members.
Next, we prioritize understanding our customer requirements.
By gathering feedback and really listening, we ensure our end products meet or exceed expectations.
Planning should also include risk management.
Identifying potential problems early allows us to develop solutions in advance.
This proactive approach minimizes disruptions and keeps us on track.
Lastly, documenting our planning process is vital.
Written records help us track progress and make adjustments as needed. This step ensures everyone is on the same page and working towards common quality goals.
Principles and Methods of Quality Assurance

In quality assurance (QA), our main goal is to make sure that products and services meet specific standards by planning and controlling processes.
We focus on using effective methods to prevent defects and ensure quality from the start of a project.
Key Quality Assurance Methods
We use several key methods in our QA processes.
One important method is inspection, where we regularly check the product at various stages.
Another method is testing, which involves running the product through various scenarios to find any issues early.
This helps us make adjustments before the product reaches customers.
Audits are also essential. They verify if the processes and standards are followed correctly. By doing this, we aim to ensure long-term success and quality.
We also implement process improvement, which involves regularly reviewing and improving the way we work.
This ensures our methods stay efficient and effective over time.
Quality Assurance Process vs Quality Control
In QA, we focus on planning and preventing defects by carefully designing our processes and standards.
This forms the foundation of a robust quality assurance system or quality assurance program aimed at ensuring requirements for quality are met.
This proactive approach helps us build quality into our work from the start.
The concept of quality in QA is about improving the aspect of quality related to processes, setting high standards of quality to guide our work, and adopting modern quality practices to keep defects at bay.
Quality Control (QC) is different from QA. It involves identifying defects in the final product or service, similar to a final check.
While QC focuses on detecting issues, QA ensures these issues are less likely to occur in the first place.
Quality assurance helps by establishing preventive measures that align with the importance of quality for both processes and outcomes.
We often say that QA is about developing a great process, while QC is about checking the final product.
Both are important, but QA is more about the bigger picture of improving our overall approach.
Executing Effective Quality Control
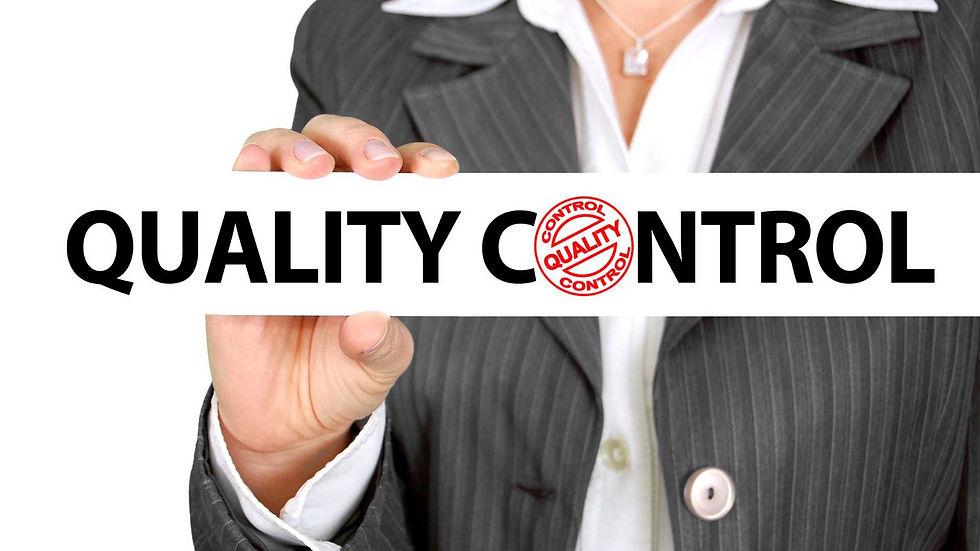
To make sure products are up to par, we use various strategies to address defects before they happen.
This includes understanding methods like statistical process control and setting up quality control procedures.
Understanding Statistical Process Control
Statistical Process Control (SPC) is a key method we use to track processes.
By collecting data during production, we can identify trends and patterns that might indicate a problem.
For instance, if we notice a consistent dip in quality at a certain point in production, SPC helps us zero in on that specific time and area.
In SPC, we use charts and graphs to visualize this data.
One popular tool is the control chart. It helps show us when a process is operating within a set range or if something is off.
This way, we can correct issues early before they become bigger problems.
Using SPC is like having a warning system. It tells us when things veer off course, so we're always working with reliable information.
This keeps our quality consistent and our customers satisfied with the products they receive.
Designing Quality Control Procedures
Creating quality control procedures is all about setting a clear path for how we check our products.
This means defining the steps everyone on our team needs to take to ensure quality.
First, we need a checklist of all the aspects of the product that need to be reviewed, like size, color, and material.
We also decide who will perform each task and how often they need to be done. This helps us stay organized and consistent.
For some products, we might test samples from a batch to see if they meet our standards. If something doesn’t measure up, we tweak our process and make improvements.
It’s important for us to train everyone involved in these tasks.
That way, every team member knows how to perform checks effectively.
Designing these procedures helps us maintain high standards across the board, ensuring we deliver the best to our customers.
Total Quality Management Concepts
Total Quality Management (TQM) focuses on maintaining quality by involving everyone in an organization's cooperation.
This approach ensures quality improvement across all areas, processes, and employees.
The Role of Total Quality Management
Everyone in the company plays a part in TQM. It’s about teamwork.
Together, we can achieve better quality by focusing on improving processes and ensuring customer satisfaction.
This involves continuous learning and adapting to change.
Key aspects include quality circles, where small groups of employees meet to solve problems and improve work-related challenges.
By doing this, we get direct input from those who know their jobs best.
Using tools like quality control charts and regular audits, TQM helps us track progress, maintain standards, and ensure that we meet customer expectations consistently.
By implementing these methods, our organization becomes more efficient and reliable.
TQM is not just about fixing issues; it’s about preventing them from happening in the first place.
Through commitment and cooperation, we create an atmosphere where quality thrives.
Software Quality and Standards
In our world of technology, ensuring software quality is key.
We need to meet certain standards and follow best practices to ensure our software is reliable and efficient.
Software Quality Assurance Best Practices
It's important to adopt effective quality assurance practices to achieve high software quality.
One fundamental practice is regular testing.
Frequent and thorough testing helps us find and fix bugs early.
We should use automated tests alongside manual testing to speed up the process and maintain consistency.
Implementing quality management software is another best practice.
This software tracks issues, manages tests, and ensures compliance with quality standards.
By doing this, we make sure our software meets the necessary quality standards and requirements.
Clear documentation of these standards is crucial.
It guides everyone involved in the development and helps us maintain a uniform approach to software quality.
Quality in Production and Development
In production and development, quality plays a crucial role.
We focus on maintaining high standards through the development process and implement methods to ensure quality in production.
It's important to have clear processes and involve the right people to meet our quality goals.
Quality Across the Development Process
During the development process, ensuring quality from the start is essential.
Bloomberg reveals that catching defects early in the development phase can reduce costs by up to 70%, as addressing issues later becomes significantly more expensive and time-consuming.
Our team, including quality assurance engineers, makes sure that each phase checks the quality of the product.
We use detailed plans and tests to catch problems early.
From the initial design to the final product, we stay focused on quality.
This means regular tests and evaluations, improving our work at each step.
Automated tests and manual reviews help a lot. They make sure the final product meets our standards.
Implementing Processes for Production Quality
Implementing processes for production quality means setting up clear steps and guidelines.
Our goal is to make sure that quality standards are met every time.
Entrepreneur research shows that companies with strong quality management systems see a 15-20% reduction in defects, leading to higher customer satisfaction and trust.
We develop these processes to match the specific needs of our production lines.
We establish regular inspections and checks.
This keeps quality consistent and helps us catch any flaws quickly.
Creating a culture where everyone values quality is also important.
We encourage feedback and continuous improvement.
Using tools and technology helps streamline these processes.
This approach allows us to focus on making quality products efficiently.
Enhancement and Improvement Strategies
To enhance quality and ensure reliability, we need strategies that focus on improvement and integration.
Continuous Quality Improvement
By using continuous quality improvement and integrating safety measures, we can boost the quality and safety of our work.
Continuous quality improvement is a method where we keep making small changes toward a bigger goal.
We look at what we do regularly and find ways to make it better.
This process involves everyone, from top managers to team members.
Checklists are very useful in this approach because they ensure we meet standards every time by enhancing performance across roles.
They guide us in following standard methods to reduce mistakes.
Seeing progress motivates us to keep refining our work, which enhances quality improvement.
Integrating Safety and Reliability
Safety and reliability go hand in hand with quality. We must adopt practices that ensure our products or services are both safe and reliable.
By integrating these into our routine processes, we minimize the risk of errors or failures.
Training plays a significant role here. It equips everyone with the knowledge and skills needed to meet demands while maintaining high standards.
If we prioritize safety procedures, our work quality improves naturally. This integration gives us a strong foundation for consistent reliability and quality.
Final Thoughts
Fostering a culture of innovation is vital for staying competitive in today’s rapidly evolving world. It’s not just a trend; it’s a fundamental driver of growth and transformation.
We’ve all seen organizations that struggle to adapt due to rigid structures and outdated practices. In contrast, an innovation-driven culture embraces change, encourages creativity, and fuels progress.
Key Benefits of an Innovation Culture:
Accelerated problem-solving and decision-making
Increased adaptability to market demands
Enhanced employee engagement and creativity
Time to Revitalize Your Workflows
Ready for Business Process Optimization?

Are your business operations lagging behind? Team up with DoGood Agency for expert business process optimization. Allow our skilled SOP development specialists to help you build an efficient, standardized, and dynamic work environment.
Get started with a free 30-minute SOP development consultation with a member of our team. In just half an hour, you'll gain:
Fresh insights into your current operational processes
Quick-win strategies to boost efficiency
A roadmap for long-term operational transformation
Commentaires